Discover our expert insights
We like to keep our readers up to date on complex HealthTech development issues, the latest industry trends and updated guidelines to help you to solve a problem or make an informed decision, and learn how VCLS can provide you with tailored solutions to effectively move your product development forward.
Filter by
1/4 Types of insight
0/14 Categories
Sort by
No select
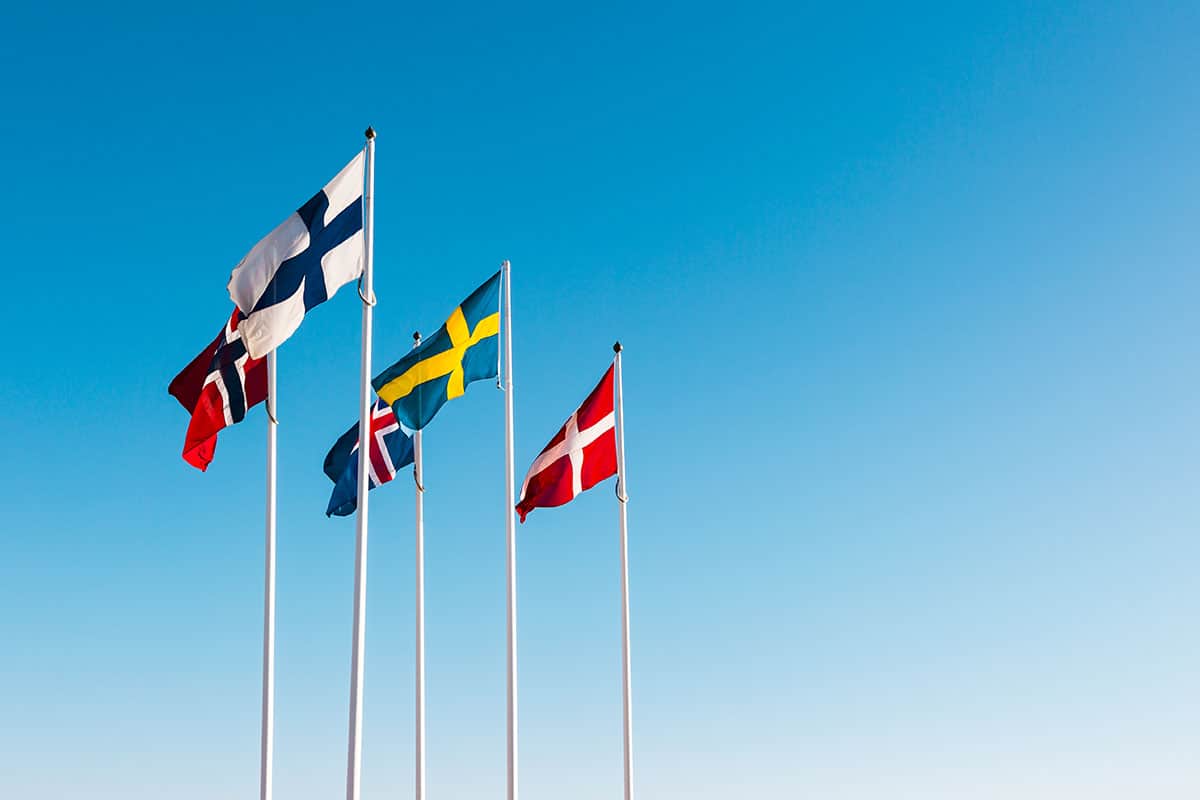
The Nordic Opportunity: Turning Real-World Data in...
No results